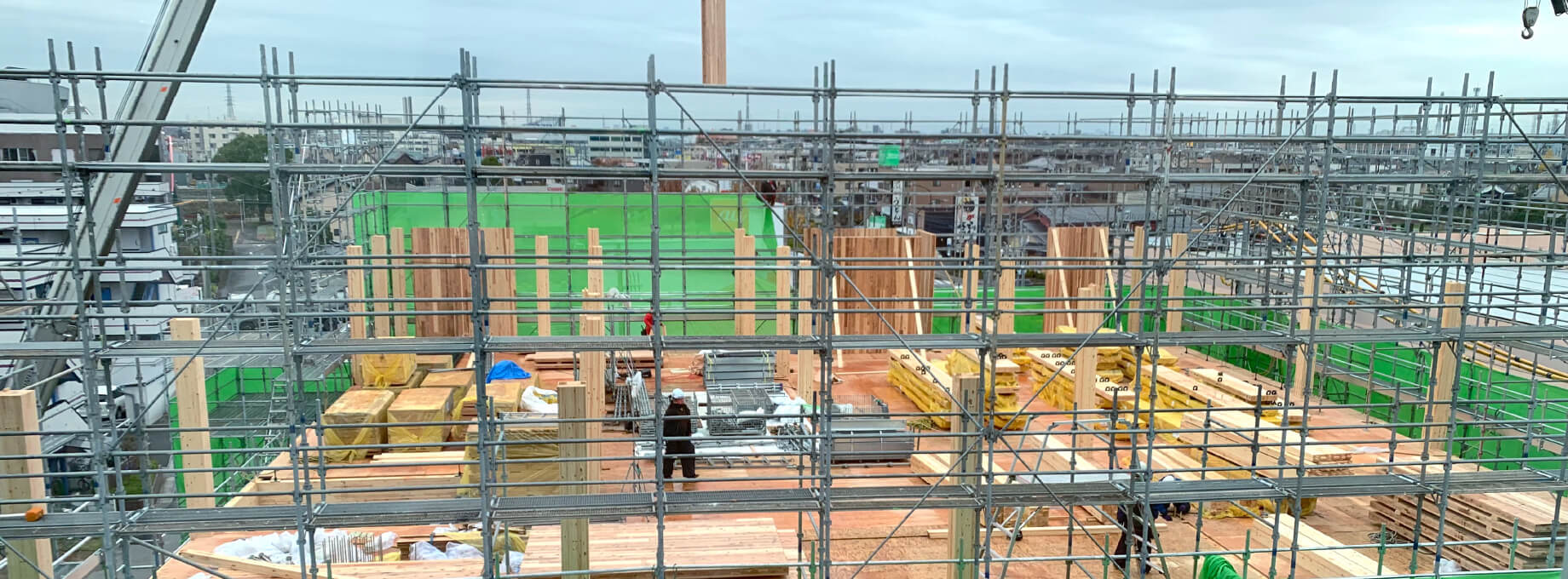
Project Story #04
木造非住宅建築への挑戦。
ポラスグループの力を
結集した、新社屋
「テクノキューブ」の建設。
2020年3月、ポラスグループにおいて住宅の品質保証やアフターメンテナンスなどの事業を手掛ける住宅品質保証の新社屋「テクノキューブ」が完成した。隣接地に、木と鉄の木質ハイブリッドの躯体で建てられた同グループのオフィスビル「ウッドスクェア」が建つことから、それとの調和を考慮しつつ、「純粋な木造」でのオフィスビルが建設された。訪れる人の目に飛び込んでくるコーナー部分をカーテンウォールとし、柱や梁などの構造材が見える状態にすることで、木の構造躯体の持つ力強さと、優しさや柔らかさを表現している。ポラスグループは数年前から「木造非住宅建築」の取り組みを加速させているが、「テクノキューブ」はその象徴的存在でもあり、ポラスグループの技術力、ノウハウを結集させた建物となった。
Member
-
ポラス暮し科学研究所 構造グループ
照井 清貴Kiyotaka Terui
1990年入社
入社後、大工を目指して訓練校に入学。入社4年目、ポラス暮し科学研究所に異動となり、生産合理性を高める工法開発に従事。その後、構造に関する研究を進め、パネル構法や柱と梁の接合システム、耐力壁など、構造部材の商品開発に取り組み、現在に至る。
-
プレカット事業本部 構造設計部 システム統括係
板澤 昂史Takashi Itazawa
2006年入社
入社以来、一貫してプレカット事業に従事。入社から約10年、プレカットにおけるCAD設計を担当した後、その外注先であるベトナムや中国などで、構造計算の教育・主導に従事。2020年より現職。
-
木造建築事業部 南部事業支店 設計室
川上 竜之介Ryunosuke Kawakami
2013年入社
入社後、分譲住宅の現場監督を経て、注文住宅の現場監督に。2017年、一級建築士の資格取得。翌18年から非住宅である木造施設の現場監督に従事。2020年、かねてからの希望であった設計室に異動となり、現在は注文住宅の設計を担当している。
chapter
01
政府が進める木材利用の促進。
自社建物で「木造非住宅建築」の
検証を進める
2010年10月、「公共建築物等木材利用促進法」が施行された。同法の目的は、木材の利用確保を通じて林業の持続的かつ健全な発展を図り、森林の適正な整備および木材の自給率の向上に寄与することだ。そのために、特に3階建て前後といった低層の公共建築物については木造化を検討することが明文化され、またそれ以外の建物においても、木造率が低く、潜在的な需要が期待できる公共建築物に重点を置いて木材利用を促進することが定められた。
さらに、世界で「脱炭素社会」や「カーボンニュートラル」(CO2排出と吸収がプラスマイナスゼロ)の実現を目指した動きが増えていることにも後押しされ、民間での木造化の動きは活発化。国内が人口減少社会に突入する中、今後住宅市場がシュリンクしていくことは否めない事実ではあるものの、政策として木造の利用促進が打ち出されたことは、木造住宅メーカーにとっては新たなビジネスチャンスの到来ともいえるのだ。
ポラスグループにおいても、法律施行直後から「木造非住宅建築」の検討が始まり、すでに保育園や福祉施設、事務所等などで堅実に実績を築いてきただけでなく、自社グループの建物では「木造非住宅建築」のノウハウや新たな技術を培うべく挑戦を続けてきた。その最初の建物が、2016年2月に竣工した「ポラス建築技術訓練校」だ。3階建ての事務所棟および平屋建ての実習棟からなるもので、木造施設プロジェクトにおける「実例モデル」として建設。国土交通省からサステナブル建築物等先導事業に採択されている。続いて、グループ会社 ガーデンヒルズの新社屋、木造3階建ての「ウッドガーデン」を建設した。いずれも「木造非住宅建築」として高品質を実現したが、コストや工期の面で課題が残った。それらの課題を解決すると同時に、ポラスグループにおける「木造非住宅建築」のシンボル的存在として構想されたのがグループ会社 住宅品質保証の新社屋「テクノキューブ」である。
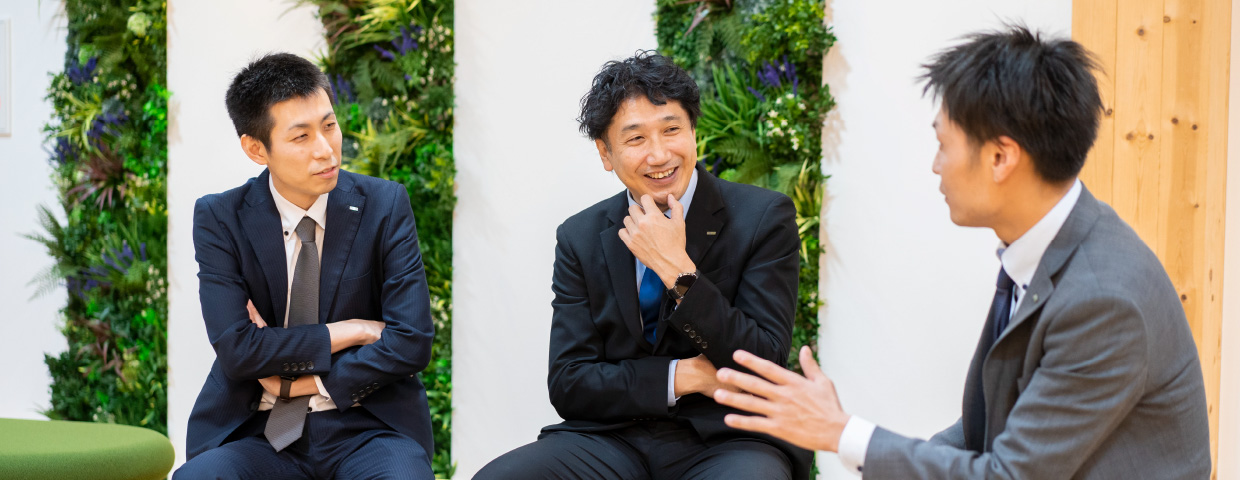
chapter
02
オリジナル構造部材
「合わせ柱」「重ね繋ぎ梁」
「CLT構造壁」の採用
木材は、比強度で比べると圧縮強度では鉄の約2倍、引張強度では鉄の約4倍といわれている。 地震によって建物が受ける地震力(振動エネルギー)は、建物の重さに比例するため、日本のような地震の多い国では、軽くて、強い木材で建物を作ることが適しているのだ。こうした素材としての強みを最大限に活かし、ポラス暮し科学研究所が開発したのが、「合わせ柱」「重ね繋ぎ梁」「CLT構造壁」といったオリジナル構造部材だ。これらの開発・採用が、テクノキューブを実現に導いたといっても過言ではない。その開発を担当したのが、同研究所構造グループの照井清貴である。
「今回の大きな課題であったコストと工期の圧縮をクリアするべく取り組んだのは、『特注扱いとなる構造部材に、いかに住宅に用いられている一般流通材を適用するか』ということでした。そこで、幾度とない実証実験を重ねながら、同等の強度を実現する構造部材を開発。それが、流通材の柱を9本組み合わせて1本の大きな断面にする『合わせ柱』と、流通材の梁を2段以上に積み重ねて、直列に繋いだ『重ね繋ぎ梁』でした。当初は住宅に比べ、非住宅は何倍も大きな部材が必要となるため、特注部材を発注する必要がありましたが、住宅用の一般流通材を適用したことで、生産・調達コスト等の圧縮が実現しました」(照井)
さらに、もう一つの構造上のポイントが「CLT構造壁」の採用だ。CLTとはラミナを直交に積層接着した木質材料のことで、現在林業及び木材産業の成長産業化を目的として政府が活用を推奨している構造材でもある。過去の木造非住宅建築の課題として耐力壁工事の工期とコストのバランスがあり、照井はCLTを利用することでこの解決を図ることを考えた。「従来の耐力壁工事の課題として、まず一つ目は、建物の主要な構造材を組み立てる“建て方”の後に耐力壁工事をまた一層目から実施しなければならないこと。二つ目は、強度を確保するには通常よりも多くの耐力壁が必要になること。三つ目は、高い強度を確保するにはより多くのビス接合が必要となり工事の手間が格段に増えることです。こうした課題をクリアするべく、CLTを建て方工事の際に同時に施工できるように独自の接合方法の開発。それにより、設置して締めるだけという簡単な接合でも高い強度と施工性を実現し、最終的には大幅な工期短縮・コストダウンにつながりました」(照井)
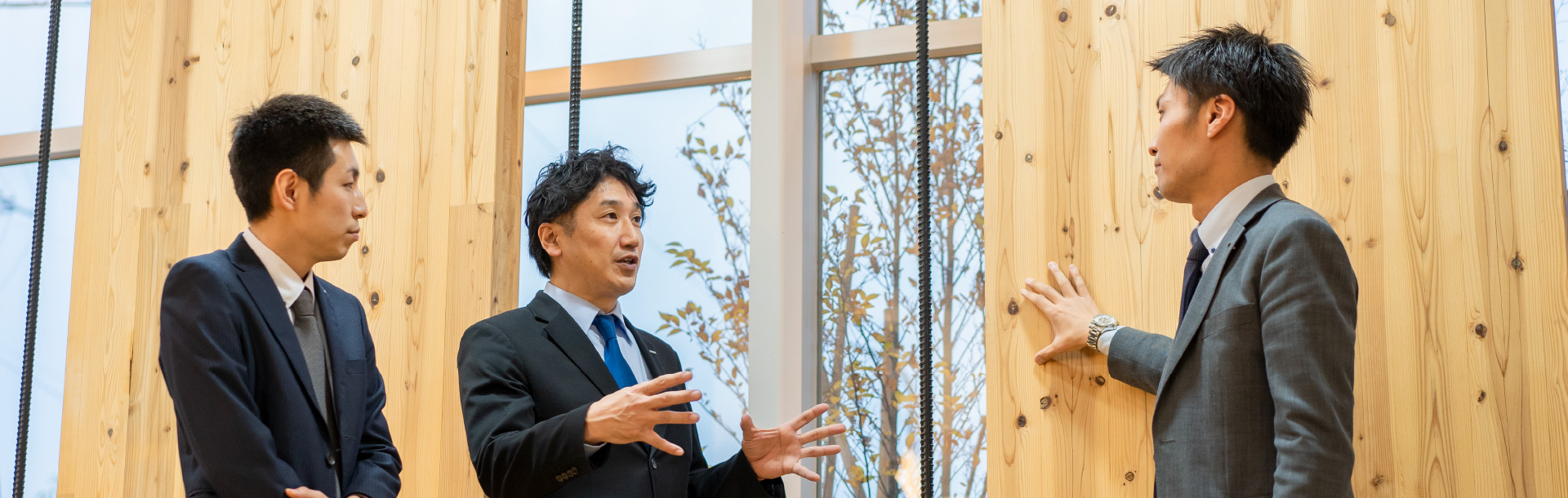
chapter
03
国内NO.1の供給量を誇る
プレカット。
蓄積された知見が生んだ
加工の最適化
今回のプロジェクトで重要な役割を担ったのが、プレカット事業部である。プレカットとは、現場での施工前に工場などで原材料を切断、接合部の加工を施すことであり、ポラスグループは、国内NO.1の供給量を誇るプレカット事業者という顔を持つ。こうしたプレカットの技術や機械は年々進化しており、最新の機械では平面図や立面図を基に加工データをCADで入力し、その情報をCAMに転送すれば自動的に切削される。自動化により、加工精度の高い柱や梁等の生産が可能となっているのだ。このプレカットに入社以来一貫して携わってきたのが、板澤昂史だ。大型のプレカット案件や木造非住宅の構造計算を数多く担当してきた経験や知見が買われ、プロジェクトにアサインされた。
「私は、研究所から送られてきた構造部材の設計図面をもとにプレカットを行うための加工用データを作成し、プレカット工場へ引継ぐという役割を担いました。最も注力したのは、加工用データの作成にあたり、設計者・プレカット工場・施工現場の3者での打ち合わせを重ね、それぞれの要求事項を的確にとらえてデータを作成すること。プロジェクト全体として、コストダウン、工期短縮がテーマとしてあったからこそ、現場での施工性を大事にプレカットのプロとしてデータを作成しましたし、プレカット工場に対して加工用データを渡す際も、加工ミスや加工に手間取らないよう、よりわかりやすく伝えることを心掛けました」(板澤)
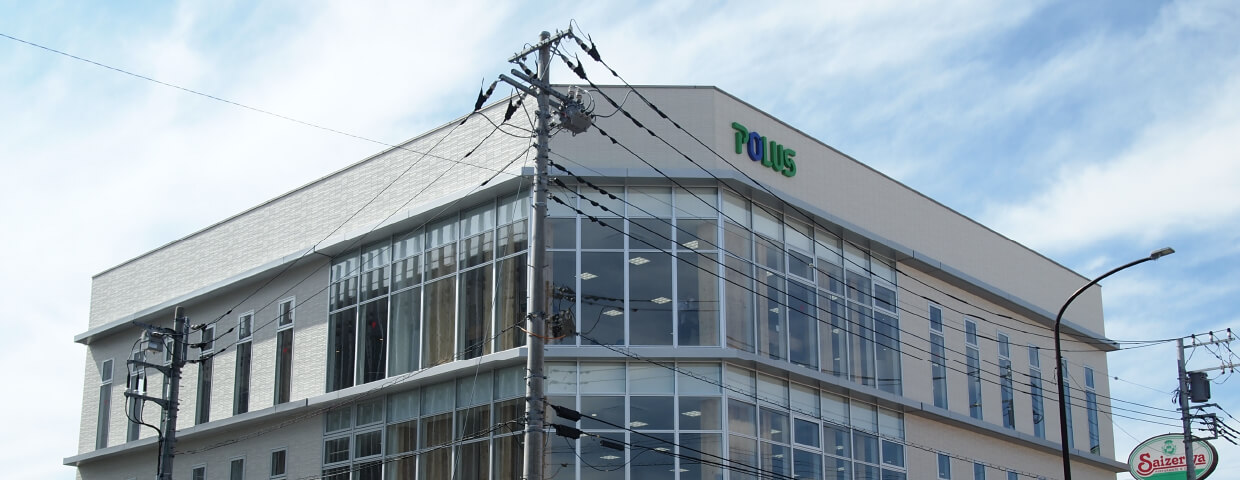
chapter
04
手探りの状態から
築き上げられた木造非住宅。
木造ゼネコンへと進化する
マイルストーンに
板澤がコントロールし、工場で加工されたプレカット材は、順次現場に納入された。その現場を監督として仕切ったのが、当時入社7年目の川上竜之介である。
「多層階としては、グループとして手掛ける最大級の建築物であり、施工知識としては木造住宅よりも鉄骨造の知見が必要とされる構造方式。これまで保育園等の木造施設物件の経験はあったものの、未知の工法・規模の建物をつくることにワクワクしたのを覚えています。木造住宅の場合、長年培ってきたノウハウや標準化された手順があるため、現場を管理することに困難さはさほどありません。しかし今回は、多層階建築であるとともに、工法を熟知している人が誰もいない状態。非住宅ならではのつくり方を、現場監督である私はもちろん、普段住宅を手掛けている大工の方々も手探りで構築していく必要がありました。」(川上)
川上が語ったのは、施工に際して立ちはだかった、いくつもの壁。何もかもが手探りの状況であるため、もちろん施工前には入念に施工計画を立てた。それでもやはり、現場では計画通りに進まないことも多かった。たとえば、柱を建てる際のレベル(高低)調整に関しても、通常の住宅の場合であれば決まった手順で進めていけばいいが、非住宅に決まった手順はない。施工しながら最適なレベル調整の方法を大工の方々と議論する場面もあったという。そんな中で川上が心掛けたことがある。
「未知の現場だからこそ、“いつも通り”は通用しません。予期せぬ出来事で状況が変わったとしても、そのたびに一つ一つ自分の頭の中で詳細に計画を組み直しながら、スムーズに進行できるように努めていました。また、グループとして先進的事例になることから、建物を単に完成させるのだけでなく、後に続く非住宅建築にもノウハウを少しでも継承できるよう、丁寧に管理することにこだわりました」(川上)
こうして、2019年8月に着工した「テクノキューブ」は翌2020年3月に竣工。約8ヶ月という期間は、その規模を考えれば、驚異的なスピード施工であることがわかるだろう。構造グループの照井は、振り返ると大きな感慨があるという。
「竣工までの施工の現場、納品されたプレカット材に接し、ポラスグループの“つくる力”、すなわち“つくる人”の凄さを再認識しました。プロジェクトに関わった板澤さんや川上さんをはじめとして、すべての人が最大限に力を発揮した、美しい連携プレーだったと思います」(照井)
プレカットを担った板澤は、現在新たな取り組みを進めている。
「これまではプレカットCAD設計、構造計算を中心に携わってきましたが、現在はプレカットCADと他のシステムをつなぐことでの業務効率化の検討等を進めています。また今後は、CADとIT技術を組み合わせた新しい設計手法の開発にも取り組み、プレカットの側面からポラスグループの新たな価値創出を目指していきたいです」(板澤)
現場監督だった川上は、今、かねてからの希望だった設計の仕事に就いている。
「竣工したとき、見事な構造美が実現できたという実感がありました。木造の強み、魅力は絶対にあると確信していますから、今後は、これまでに現場監督として培ってきた知見を総動員しながら、設計士として木造の可能性を追求していきたいと思っています」(川上)
「テクノキューブ」――それはポラスグループの「木造非住宅建築」の一つの答えであり、今後、中大規模木造建築へ、そして木造ゼネコンへと進化するためのマイルストーンとなったに違いない。